Scroll ned
Vi ændrer den måde vores kunder udvikler og tester
Vi skaber værdi for vores kunder med løsninger tilpasset deres behov, uanset om det er til produktudvikling eller et nyt testsystem.
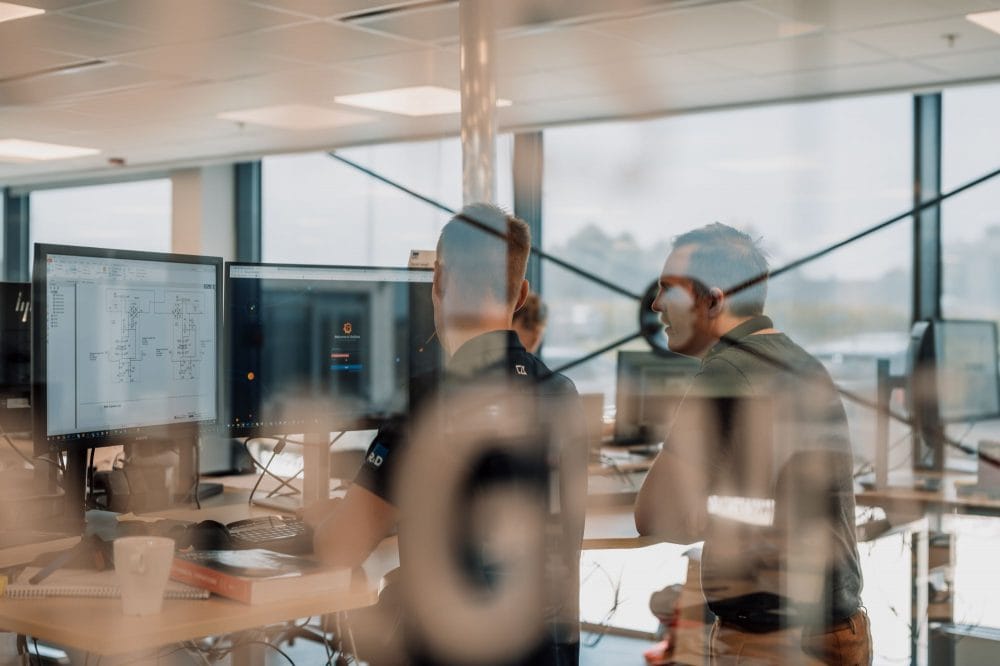
Karriere
Vi er altid på udkig efter engagerede medarbejdere, som stræber efter at løse komplekse problemstillinger i et professionelt og socialt miljø.
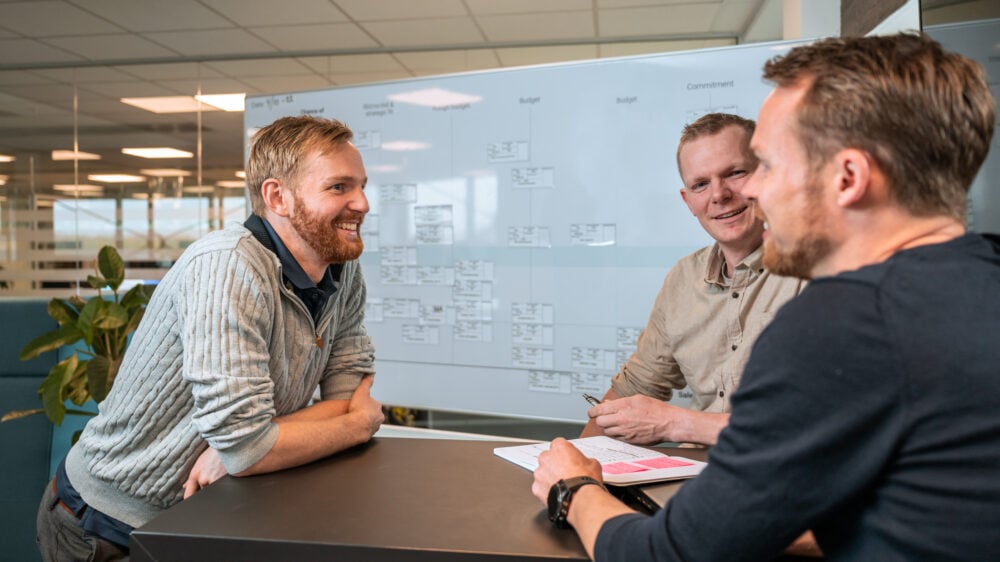